Cladding of metals overview
Metal cladding is a material formed by using various composite technologies to achieve the metallurgical bonding of metals with different properties at the interface. The bonding area shows undulating metallurgical bonding characteristics.
Characteristics of metal cladding
Metal cladding is a material formed by using various composite technologies to achieve the metallurgical bonding of metals with different properties at the interface. The bonding zone is characterized by wavy metallurgical bonding.
Advantages of metals cladding
Metal cladding of the base material to meet the mechanical properties of the organization, composite plate to meet the corrosion or wear resistance, greatly improving the thermal expansion properties of a single metal material, good fatigue properties, fracture toughness, wear resistance, corrosion resistance, electrical properties, magnetic properties, and many other properties.
Application fields of metal coated metal sheets
Metal-coated metal sheets are widely used in automobiles, electronics, construction, home appliances and other fields. They can provide features such as beautiful appearance, enhanced corrosion resistance and electrical conductivity to meet the needs of different fields.
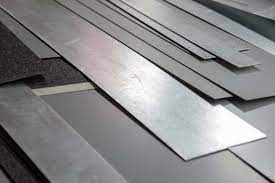
Cladding of metals
What is an explosive composite plate?
Explosive composite plate generally refers to the explosive metal composite plate. The prepared composite plate is placed on the substrate, and then a layer of explosives is laid on the composite plate. Using the instantaneous ultra-high pressure and ultra-high speed impact generated by the explosion of explosives, a solid metallurgical bond between the metal layers can be achieved.
Features of explosive composite plate
Explosive composite plates are manufactured by placing the composite plate on the substrate and then laying a layer of explosives on top of the composite plate. Using the instantaneous ultra-high pressure and ultra-high speed impact energy generated by the explosive explosion, a solid metallurgical bond between the metal layers is achieved. Although the production process of the explosive composite plate is simple and flexible, it has high technical requirements. Substrate performance (toughness, impact performance, etc.), explosive performance (stability, safety, etc.), initial parameters (explosive unit area, base plate spacing, etc.), and dynamic parameters (collision angle, base plate collision speed, etc.) is difficult to accurately control, the selection of composite plate and the system directly affect the yield and quality of the finished product.
The composite interface consists of a direct bonding zone, melting layer and vortex. The bonding interface has atomic diffusion, and the bonding zone has severe plastic deformation and process hardening. The bonding surface has a wavy structure, which contributes to the bonding strength and tensile strength.
Company profile
Synthetic chemical has been dedicated to metals cladding for ten years and is a professional company with supply and marketing integration. The company has a professional technical department and quality supervision department, a well-equipped laboratory with advanced testing equipment, and an after-sales customer service center.
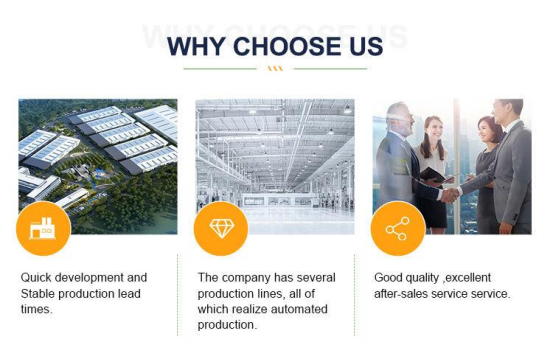
Storage conditions
1) Maintain a dry area at the temperature of room.
2) Avoid high and damp temperatures.
3) Utilize immediately following the opening of the bag inside.
Payment methods
L/C, T/T, Western Union, Paypal, Credit Card etc.
Shipment
By sea, by air, by express, as customers request.
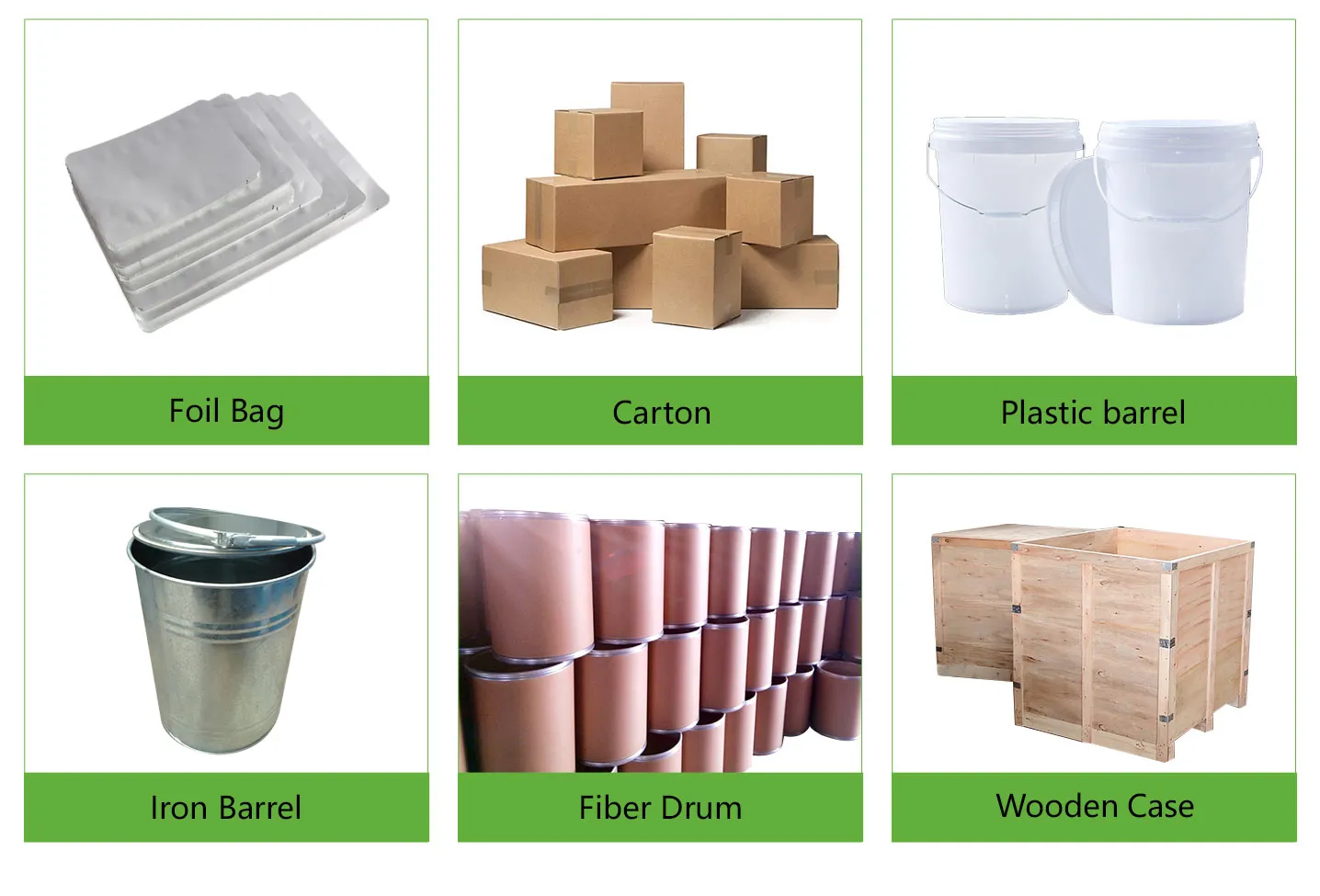
FAQ
Q1:
What is the reason why metal-coated metal plates turn black?
Re: The reasons for the blackening of the metal plated metal plate may include excessive metal impurities and organic impurities in the plating solution, insufficient additives, and too low temperature. These factors may lead to uneven plating, blackening or other quality problems.
Q2:
How to deal with the problem of blackened metal plate?
Re: Dealing with the problem of blackening of metal plated metal plates usually involves the following aspects: first, check the content of metal impurities and organic impurities in the plating solution. If it is too high, it needs to be dealt with; secondly, ensure an adequate supply of additives; finally, adjust the temperature to the appropriate range to ensure the uniformity and quality of the coating.
Q3:
What causes uneven gloss and uneven thickness of metal-coated metal sheets?
Re: The uneven gloss and uneven thickness of metal plated metal sheets may be caused by insufficient additives, uneven current distribution, unstable plating bath temperature and other factors. These problems can lead to a decrease in the quality and performance of the coating.
Q4:
How to avoid uneven gloss and uneven thickness of metal-coated metal sheets?
Re:To avoid uneven gloss and uneven thickness of metal-coated metal sheets, the following measures can be taken: ensuring adequate supply of additives, maintaining uniformity of current distribution, and controlling the stability of the temperature of the plating solution. In addition, regular inspection and maintenance of plating tanks and equipment is also very important.
Q5:
How is the corrosion resistance of metal-coated metal sheets evaluated?
Re: The corrosion resistance of metal-coated metal plates can be evaluated through salt spray tests, electrochemical tests and other methods. These methods can simulate corrosion conditions in harsh environments to evaluate the corrosion resistance of coatings.